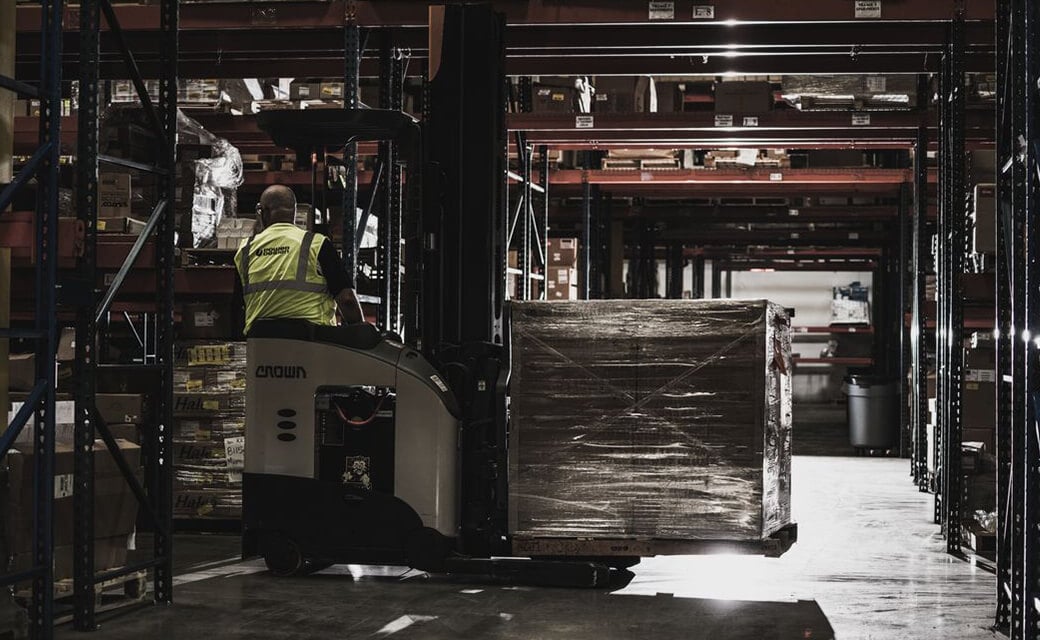
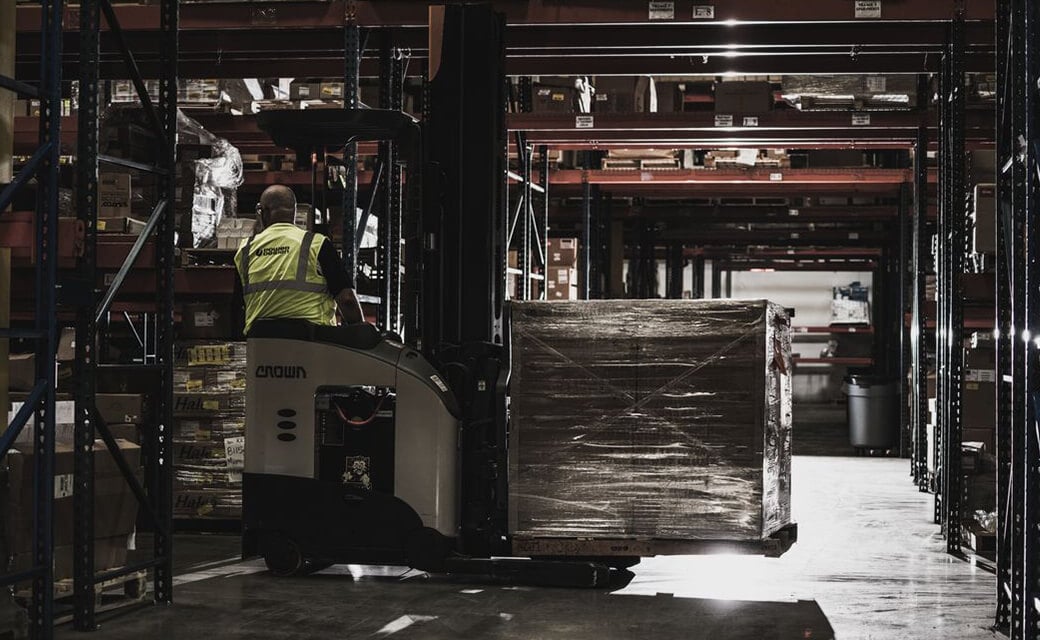
It’s no surprise that the construction industry, especially today, faces many challenges. From labor shortages, to fast-track schedules, to maneuvering through tight footprints and transporting material – these are just a few of the obstacles our workers overcome on a daily basis. Add in a nationwide pandemic and you’ve got even more to consider. But with advancing technology and innovation comes a trend that Power Design is leveraging more and more: pre-fab.
Prefabrication utilizes offsite space to remotely pre-assemble components of a building. Once transported to the jobsite, teams are able to complete a modular install in less time, and with less manpower than traditional install methods. Since so much of multi-housing construction is a step-and-repeat process with repetitive unit installs, there are many pro’s to prefab. Here are just a few:
-
Safer: Indoor material assembly makes it easier to control the health and safety of workers, which is something we’re paying extra attention to during this time. By assembling parts inside and offsite, weather and vandals no longer pose a threat in terms of damage or delays. Less manpower in a room at one time = better social distancing, too!
-
Faster: According to Brandt, a pre-fabricated project can go up 50% faster than a traditional job. This is especially convenient during the rainy season, when delays in construction tend to rise, or a project with a We recently completed a pre-fab installation of the electrical panels at our project, DuPont Building – Phase II, in Wilmington, Delaware where we were able to save approximately 4 hours of labor while roughing one unit – the manpower of approximately one person for half a day.
-
Cleaner and less waste: Jobsites aren’t neat and tidy. Even the ones run by the cleanest teams still have papers, scraps, material and other miscellaneous debris rolling around. Constructing pieces offsite cuts back on waste by ensuring only the necessary amount of material is used, and encourages the recycling of scraps. It also saves on water usage!
-
Higher quality control: Material that has been manufactured in a warehouse or factory must meet predetermined quality standards before being transported to the jobsite, which allows for a more streamlined process and additional QC checks. The indoor environment also protects the building and its components from climate extremes and destruction.